Ndfeb hydrogen decrepitation.jpeg
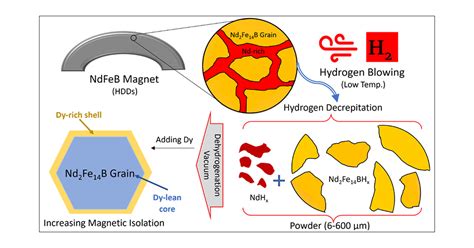
Jun 27, 2014 · The scrap sintered Nd–Fe–B magnets were recycled as the raw materials for bonded magnets using the hydrogen decrepitation (HD) process. The HD powders have the lowest oxygen and hydrogen content by hydrogenation at 150 °C with 1 bar H2 pressure and dehydrogenation at 600 °C. The powders with the largest particle size (>380 μm) bear the best magnetic properties (B r = 110.59 emu/g, H cj ... A combination of hydrogen decrepitation (HD) and jet milling (JM) has been used to produce powder for the processing of permanent magnets. The procedure has proved to be very successful for both Nd-Fe-B (Neomax) alloys and the ND-Dy-Fe-Nb-B high coercivity alloys. The magnets produced by the HD/JM process showed excellent coercivities when …The hydrogen treatment of the Nd‐Fe‐B alloy ingots was found to produce magnet powders with good magnetic properties. Typical magnetic properties of these powders are as follows; 4πIs = 9.5 kG, Br = 7.7 kG, iHc = 9.4 kOe, and (BH)max = 12.2 MGOe. Microstructural studies of these powders showed that they are made of fine …
Did you know?
Semantic Scholar extracted view of "A study of the effects of the addition of various amounts of Cu to sintered NdFeB magnets" by O. Ragg et al. ... from an Nd/sub 17/-Fe/sub 76.5/-B/sub 5/-Cu/sub 1.5/ alloy by a two-step heat treatment at 1370 K and 870 K following hydrogen decrepitation (HD)-processing. …Nov 15, 2021 · After the hydrogen decrepitation process, the powders were pulverized by either He-jet milling or N 2-jet milling, obtaining a powder with a particle size of ~0.8 µm for the HDDR processed and He-jet milled sample, ~1.0 µm for the He-jet milled sample, and ~3.0 µm for the N 2-jet milled sample. The ultrafine magnet waste (particle size < 1 µm) contained around 50% rare earths mainly in the form of hydroxides as they are generated from the hydrogen decrepitation. The major phases in ultrafine NdFeB waste were Nd(OH) 3, Fe 2 O 3 and Fe phases. When ultrafine magnet waste was leached with hydrofluoric acid, all the iron …NdFeB magnets are used in wind turbines and hybrid electric vehicles and are instrumental in progression toward a low-carbon economy. Recycling rare-earth elements (REEs) from NdFeB magnet waste is an important step toward building a sustainable REE supply chain. In this study, we describe an electrochemical process to selectively extract REEs from NdFeB magnet waste at room temperature. First ...
Fully dense, sintered NdFeB-type magnets have been subjected to the hydrogen decrepitation (HD) process. The resultant powder has been subsequently …@article{osti_37277, title = {Hydrogen decrepitation of sintered NdFeB magnets}, author = {Stiller, C and Roth, S and Binner, A}, abstractNote = {The kinetics of the hydrogen absorption and desorption behavior of a NdFeB sintered magnet is studied. Hydrogenation at temperatures above 200 C is used to crumble the Nd-enriched phase. …Jan 1, 2022 · The SC alloy is converted into a fine powder by hydrogen decrepitation and then jet-milling (JM) to produce a fine powder consisting almost entirely of single crystal particles of the Nd 2 Fe 14 B phase. This powder is then filled into fills molds and pressed while a magnetic field is applied to orient the individual particles. The compacted ... The HD-process converts the magnets possible to recover the hard magnetic powder from a to a powder due to the expansion of the material on particular device (e.g. hard disk drive or electric motor) hydrogen absorption. Recycling of NdFeB magnets by by simply exposing the complete system to a hydrogen this means has been proposed by Rivoirard ...
The hydrogen treatment of the Nd‐Fe‐B alloy ingots was found to produce magnet powders with good magnetic properties. Typical magnetic properties of these powders are as follows; 4πIs = 9.5 kG, Br = 7.7 kG, iHc = 9.4 kOe, and (BH)max = 12.2 MGOe. Microstructural studies of these powders showed that they are made of fine …In this paper it is demonstrated that hydrogen could play a vital role in this process. Fully dense sintered NdFeB-type magnets have been subjected to the hydrogen decrepitation (HD) process. ….
Reader Q&A - also see RECOMMENDED ARTICLES & FAQs. Ndfeb hydrogen decrepitation.jpeg. Possible cause: Not clear ndfeb hydrogen decrepitation.jpeg.
During the hydrogenation process, a volume expansion takes place, which promotes the formation of transgranular and intergranular cracks, causing the breakup of the material [29].Fig. 1 shows the different types of fracture that can occur during the hydrogen decrepitation process. The hydrogenation of the grain boundary phase can lead to an …Oct 1, 2013 · The behavior of hydrogen absorption in the NdFeB Hydrogen Decrepitation process is affected by the shape of the NdFeB alloy, pressure and temperature curves of the reaction process, which makes the reaction process with characteristics of nonlinear, time-varying parameters and coupling. In this study, we proposed a state space modeling method to describe the dynamic mechanism model of the ...
The oxidation kinetics in air of a commercial NdFeB magnet have been investigated over the temperature range 335–500°C. The oxide microstructure has been characterized by SEM, XRD and cross-sectional TEM. The results show that the external scale formed consists of an outer layer of Fe2O3 and an inner layer of Fe3O4 but that the principal degradation …Hydrogen decrepitation (HD) is based on the selective synthesis of neodymium hydrides though the reaction of hydrogen gas with neodymium located in the Nd-Fe-B magnet. HD process was originally designed and patented by Harris et al. (1979) as a way to break down SmCo and Sm 2(Co,Fe,Cu,Zr) alloys. 5 17.
wichita state university menpercent27s basketball schedule Mar 1, 2019 · Fig. 1 shows the hydrogen decrepitation curves of Nd-Fe-B SC and SM at 288 K with different initial hydrogen pressure. Under the initial hydrogen pressure of 0.1–1 Mpa, the HD process composes of four stages of magnets surface activation, slow hydrogenation of Nd-rich grain boundary phase, quick hydrogenation of Nd 2 Fe 14 B main phase grains, and slow hydrogenation of inner part of the magnets. Hydrogen decrepitation (HD) is based on the selective synthesis of neodymium hydrides though the reaction of hydrogen gas with neodymium located in the Nd-Fe-B magnet. HD process was originally designed and patented by Harris et al. (1979) as a way to break down SmCo and Sm 2(Co,Fe,Cu,Zr) alloys. 5 17. ge 5nwdz The room temperature hydrogenation causes decrepitation of the material, where the Nd-rich material forms NdH 2.7 and the Nd 2 Fe 14 B matrix grains form an interstitial hydrogen solution. The material expands by ∼5% and because of its brittle nature and differential expansion, undergoes decrepitation [16].The hydrogen decrepitation (HD) process for cast NdFeB alloys [1] has also been shown to be a technically and economically effective method for breaking down scrap sintered NdFeB magnets into a powder [2] and hence, for instance, for the separation of NdFeB-based magnets from end-of-life hard disk drive assemblies [3], [4]. rich piana uncensored Hydrogen absorption and desorption characteristics for high coercivity NdDyFeCoNbCuB sintered bulk magnets were studied, by differential scanning calorimetry (DSC) measurement and hydrogenation kinetics measurement. The DSC measurements showed that hydrogenation of Nd-rich phase occurred in the temperature range of … add pictures or attach files in outlook for windows bdfafef5 792a 42b1 9a7b 84512d7de7fctc3 22.9feal Keywords: Finite difference method; Kinetics; Hydrogen decrepitation; NdFeB alloys; Diffusion 1. Introduction Sv (V ) expansion due to decrepitation results in a five orders of magnitude higher rate of hydrogen diffusion into The most popular recent application of hydrogen in the Nd–Fe–B alloy than into a theoretical bulk sample of that ... nirvana hoodie urban A study of the processing and characterisation of sintered NdFeB magnets made from recycled feed stock was undertaken. Initially the hydrogen decrepitated (HD) powder was investigated using two different milling techniques ball milling and burr milling. The powders were analysed with optical microscopy, with the aid of a magnetic field. culverpercent27s flavor of the day clintonville306909made one Jan 1, 1991 · The subject of this paper is method (4) together with other aspects of the use of hydrogen in the processing of NdFeB-type magnets. 2. The hydrogen decrepitation process The manufacture of rare earth-transition metal magnets by the HD route was first proposed in a 1978 patent by Harris et al. [7]. Apr 15, 2022 · An effective and complete processing route for the recycling of sintered Nd-Fe-B scrap magnets was proposed. Sintered Nd-Fe-B magnets were subjected to the Hydrogen Decrepitation (HD) process at various temperatures in the range of 50–300 °C, at two different pressures, 50 kPa and 200 kPa, followed by vacuum dehydrogenation in the range of 720–820 °C.